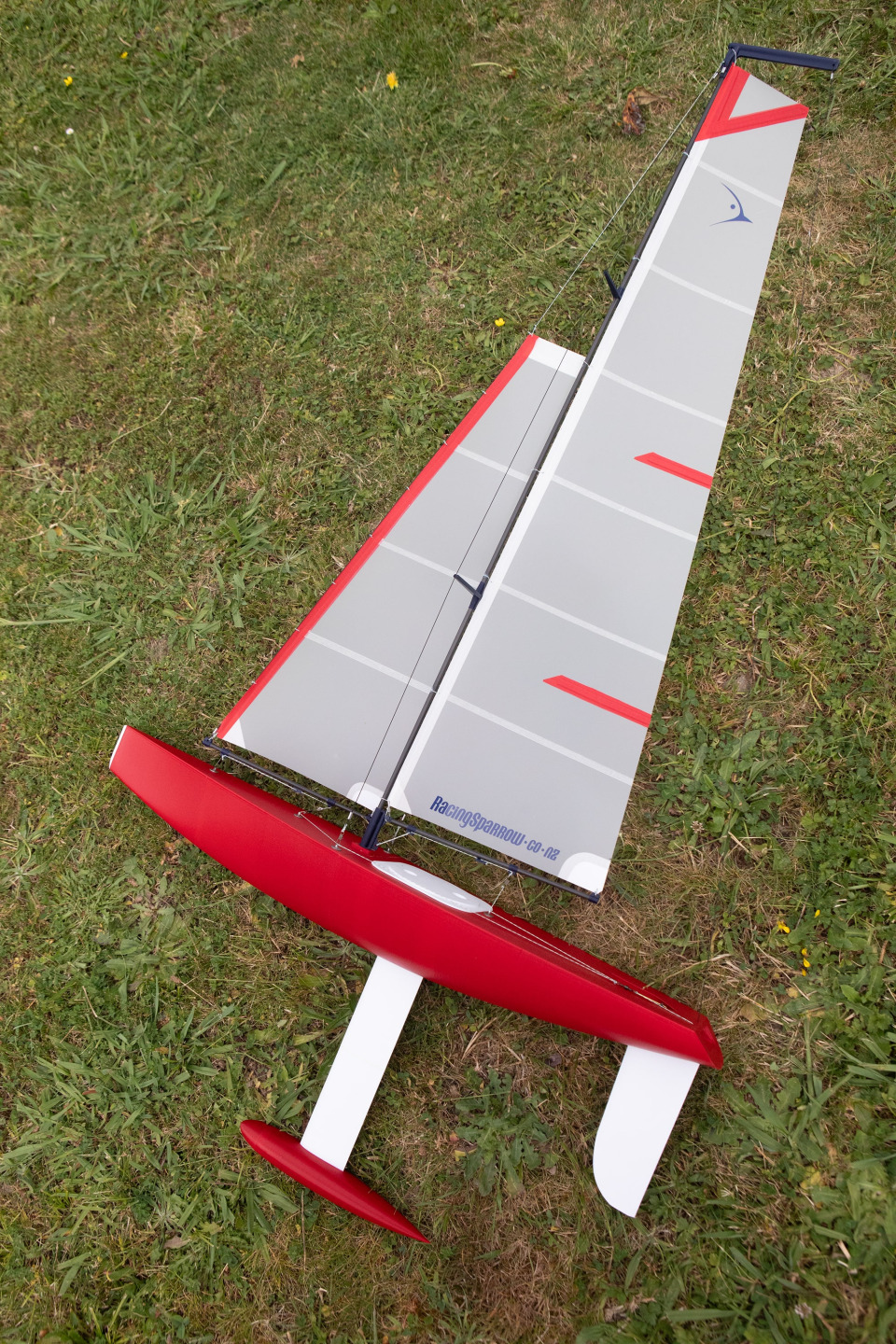
Print your own radio controlled sailboat
Following on from the successful balsa Racing Sparrow there is now also the option to 3D print a Racing Sparrow RC sailboat yacht. There are two models to build, 760 and 1000mm sailboats.
Questions? email info@racingsparrow.co.nz
Key design features:
RS760, 950 mast 0.85Kg bulb
RS1000, 1250 mast, 2Kg bulb
- Hull printed in 4 parts(760), 5 parts(1000)
- Printed rig fittings
- Twist hatch for waterproofing
- Bulb shell in 2 parts, filled with lead shot
- Keel in 2 parts, with carbon reinforcement slots
- Uses standard servos for 2-channel RC
- Minimal build time required
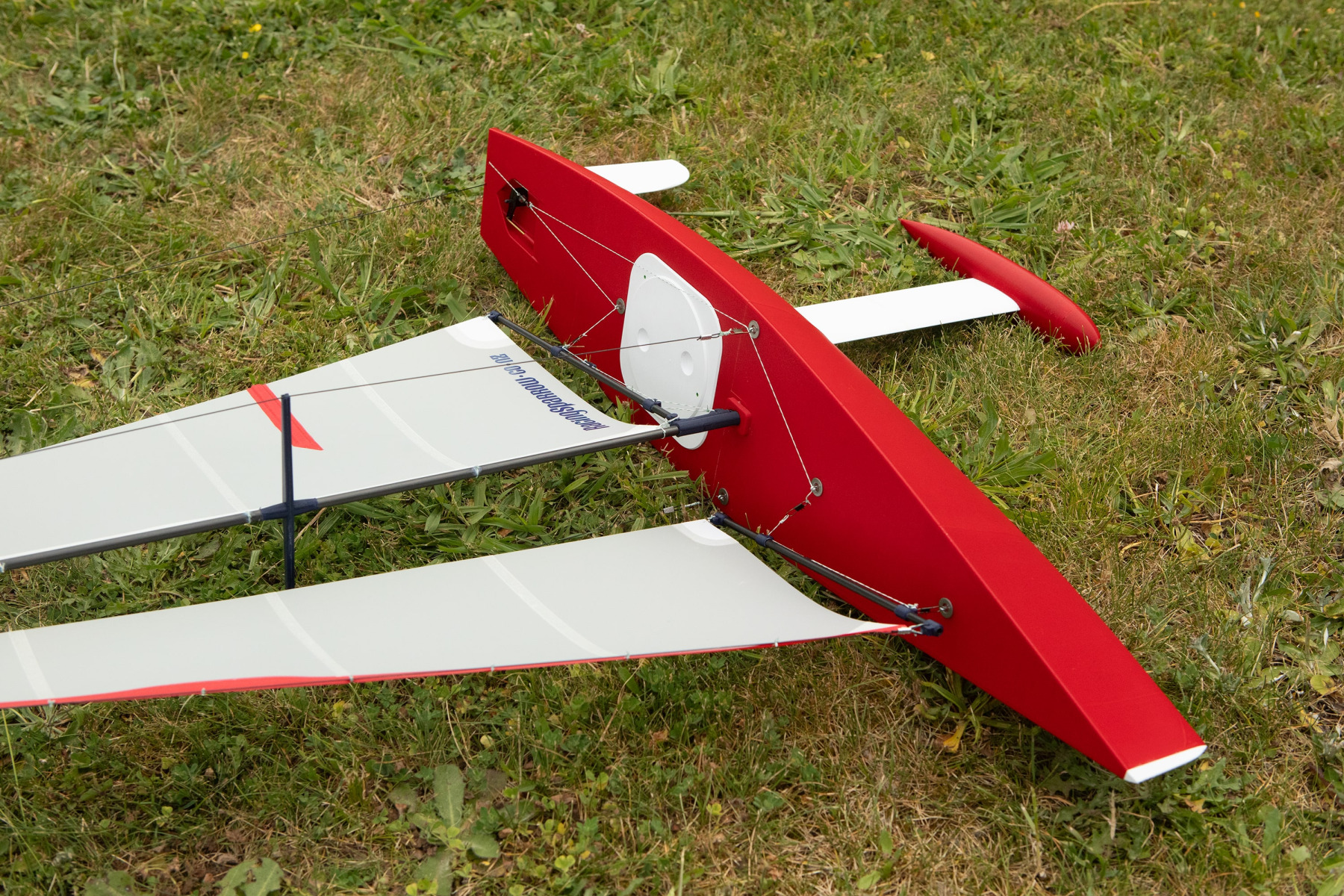
Comprehensive Instruction Manuals 760 & 1000 versions
Both the RS760 & RS1000 designs have instruction manuals which have sail plan, materials list, electrics list and more. This 3D construction method is a very fast way to make a good model yacht and the manuals makes it easy.
Download the instructions:
RS760 Instructions & Materials
RS1000 Instructions & Materials
Materials & Electronics
To complete the project you will need to source various carbon fibre rods and other raw materials like lead shot and also electronics. On the materials page I am building a list of suppliers from around the world where you can buy these materials to build your yacht.
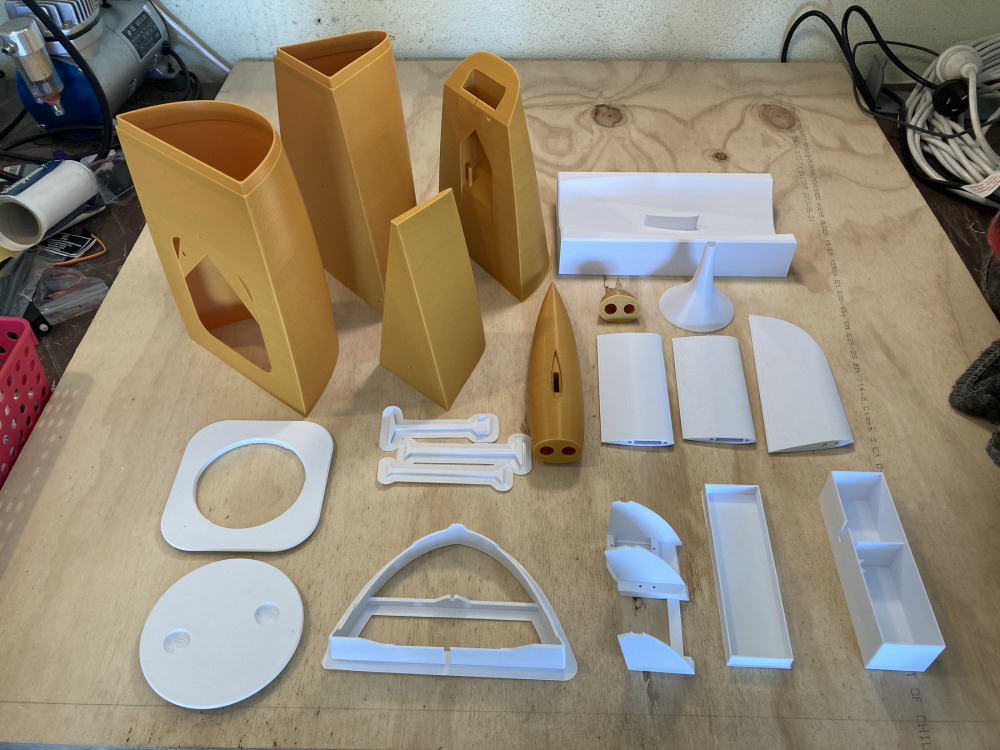
Customer Feedback
Chris, USA
It sails as good or better than my DragonFlight95. Whatever you did, you did it right. I have a very small swimming pool (8 foot by 20 foot rectangle) and I was doing figure eights just fine! Everyone at work is motivated to start building too!
Mike, Texas USA
The parts printed just fine for me on my Bambu Labs printer and were easy to assemble with superglue. Filling the hollow printed bulb with lead shot and epoxy worked well. It’s a great way to get a streamlined keel bulb without having to cast one. The kit is easy enough to print that I ran one off for a friend of mine with little trouble.
You could probably set up the rig and go sailing as the hull came off the printer, but I chose to fair and paint mine. I used drafting film and spinnaker tape to make the sails which worked well on my 1M balsa Sparrow. The 3D printed hull was the easy part as I spent more time on the sails and rigging.
All in all, it was a fun project to build. 3D printing sure gets you a finished hull a lot quicker than plank on frame or stitched plywood.
I used PLA filament for the whole project. I will have to be careful about leaving in the car in the summer or it’s likely to deform. Maybe the next one will be out of PETG.
Roland Beverley, UK
I was a beta tester for the 3D printed Racing Sparrow, working with Bryn remotely, via email, to test how the pieces printed and went together. Hence my build of the boat was experimental in parts and I took my time over it so that feedback could be given. Having said that, it was remarkably straightforward to build. Prints are very strong in PLA+ and fit well, requiring no supports.
I was apprehensive about my first sail, e.g. would the boat be controllable? Would it be dry? I need not have worried! She barely shipped a drop of water and was very easy to sail, despite my amateurish sail construction and minimal experience with model yachts. The large rudder gives plenty of authority, there is good upwind performance even without fine tuning and the rigging is simple yet robust. Indeed when my jib sheet came undone (my bad knot) and I lost my jib, she still sailed very well for a controlled recovery.
You can't lose with this boat. The parts are accessible and cheap, the build is a simple, clean and enjoyable experience (it's like making your own kit, then assembling it!) and she sails fantastically well, whether you want to play, learn or race.
What is the 3D Racing Sparrow all about?
What’s the difference between RS760 and RS1000?
Feature | RS760 | RS1000 |
---|---|---|
Hull Length | 760mm | 1000mm |
Mast Height | 950mm | 1250mm |
Keel Bulb Weight | 0.85kg | 2kg |
Hull Sections | Printed in 4 parts | Printed in 5 parts |
Filament Needed | Approximately 1 roll | Approximately 2 rolls |
Printer Bed Size Required | 200 x 200 x 210mm (XYZ) | 210 x 210 x 245mm (XYZ) |
What kind of 3D printer is best?
Most home 3D printers will be able to print the RS760-3D as the build plate size needed is only 200 x 200 x 210mm - xyz.
For the RS1000 a printer with plate dimensions of 210x210x245mm - xyz. The 1 meter sparrow requires a slightly larger printer which is still very common.
When looking for a printer look for build size, self levelling, wifi capability. Many printers now have all those features which make the experience very stress free.
I use a Creality K1 Max which is an enclosed high quality but still considered a home hobby machine. The enclosure helps keep temperatures more stable in my cold garage. If using inside then an enclosure is possibly overkill.
Can I buy the files and take them to the local 3D printer?
Yes you sure can. We don't mind how you print your boats! There are many local 3D printing companies who can print the boat parts for you and you spend a few hours building!
What will I need to finish the 3D printed build?
To finish you need:
For worldwide suppliers links try the materials page
Both the RS760 & RS1000 boats require similar parts just different dimensions. You will need Sail and Rudder Servos, receiver and transmitter. You will need carbon tubes for the mast and booms. The sails are made from Mylar and use spinnaker repair tape for attachments. Other small fishing products are used for the rig stays and connections. You will also need CA super glue and Epoxy. The bulb requires some gun shop lead shot to be used as ballast. For a comprehensive materials list for each boat design please download the instructions on this page.
What 3D printer settings are needed?
Print Settings
- Nozzle: Standard 0.4mm
- Wall Line Count: 3
- Top Layers: 4
- Bottom Layers: 4
- Infill: 35%
- Print Speed: 180mm/s
- Bed Adhesion: Wide brims inside and outside used for hull sections, no glue or sprays required
- Material: eSun PLA+
- Most parts: 224°C nozzle, 65°C plate
- Thinner/smaller parts: 230°C nozzle, 60°C plate
- Enclosure Temperature: ~30°C for best bed adhesion
- Retraction Distance: 0.8mm (reduces stringing)
How is the keel bulb weighted?
The bulb is a printed shell which you fill with lead shot from a gunshop. It's a very simple and creative way to create a lead bulb. Could not be easier. In New Zealand lead shot can be purchased from this online store.
How are the sails made?
The sails are both one piece mylar film. No sewing or double sided tape needed. You can use many materials such as grow shop mylar reflective film, architectural drafting film or ripstop nylon. What ever you choose simple flat sails work well. No need to build special complex sails. The one piece sails naturally create a nice aerofoil shape with the help of some battens on the trailing edges. Simple!
Do I need to waterproof the hull?
No. I've done many sails now with a Racing Sparrow 3D and I have done no sealing of the printed parts. I simply super glued them together and go sailing.
I sail in sea water and have had no issues. The finish of the hull being printed is not perfect but the boat still sails really fast and a nice finish really is not needed to have a fast boat. Just build quick and get sailing!
Are there any licence restrictions when I buy the STL files?
You can print up to 5 boats with 1 printer when you purchase the STL files. If you want to print and sell boats please get in contact with me to arrange terms.
At Racing Sparrow we are not too concerned with paying a fee per boat print. We would rather the STLs allow people to build multiple boats and get more people sailing and having fun.
The main thing is that no one is making money from the STL files by selling boats, parts or reselling files. If you're not sure please email me first.
All STL files and instructions are copyright 2024 Bryn Heveldt.
3D Printed Hatch and Fittings
For both boats the hatch is a twist on hatch that keeps the water out. No tape failure keeps the sailing relaxed. All rig fittings are printed parts including a tidy gooseneck assembly which is all attached to a carbon tube mast.
RS760 6mm Mast 950 long.
RS1000 10mm Mast 1250 long.

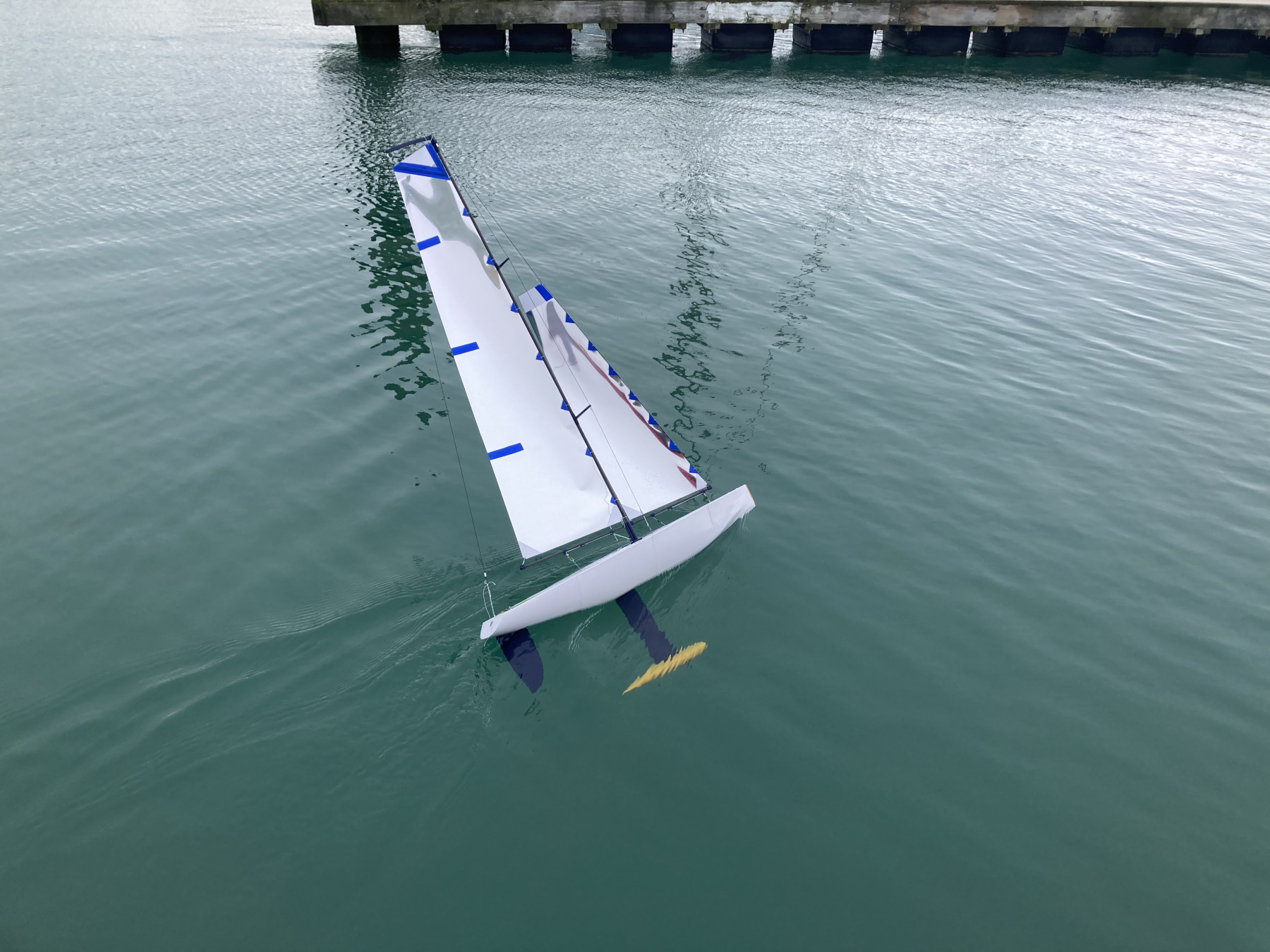
Clean Stern Design
Designed to print easily without any extra build steps the stern design integrates a water catch tray, a rudder post, a sheet return block and also a backstay attachment slot. This design makes the rear end of this boat tidy, functional and sleek.
No tape is needed to seal the boat when sailing. We've tested it in stormy conditions as well as calm and the boats are always dry inside at the end. You will be surprised how many features are packed into one 1 STL file.
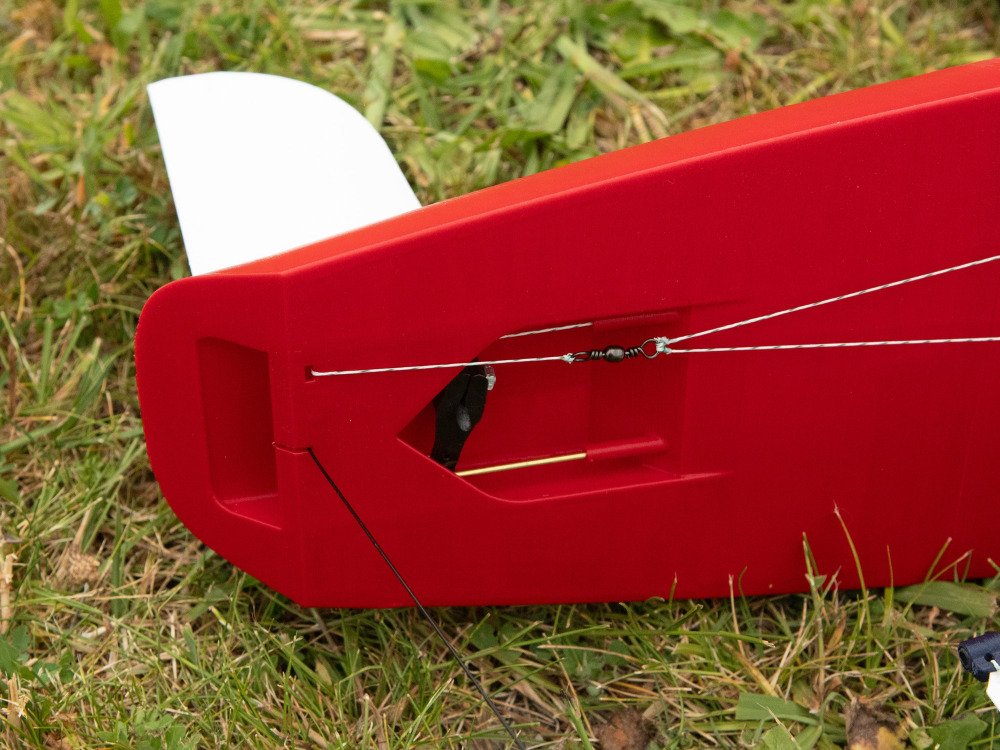
Simple Clean & Cheap Electrics Layout
The electrics used are some of cheapest servos and RC gear you can buy. No special drum winch required as the Racing Sparrow uses a standard servo with a long arm to pull the sails in and out. This keeps the costs way down. This is a key consideration of all Racing Sparrow designs.
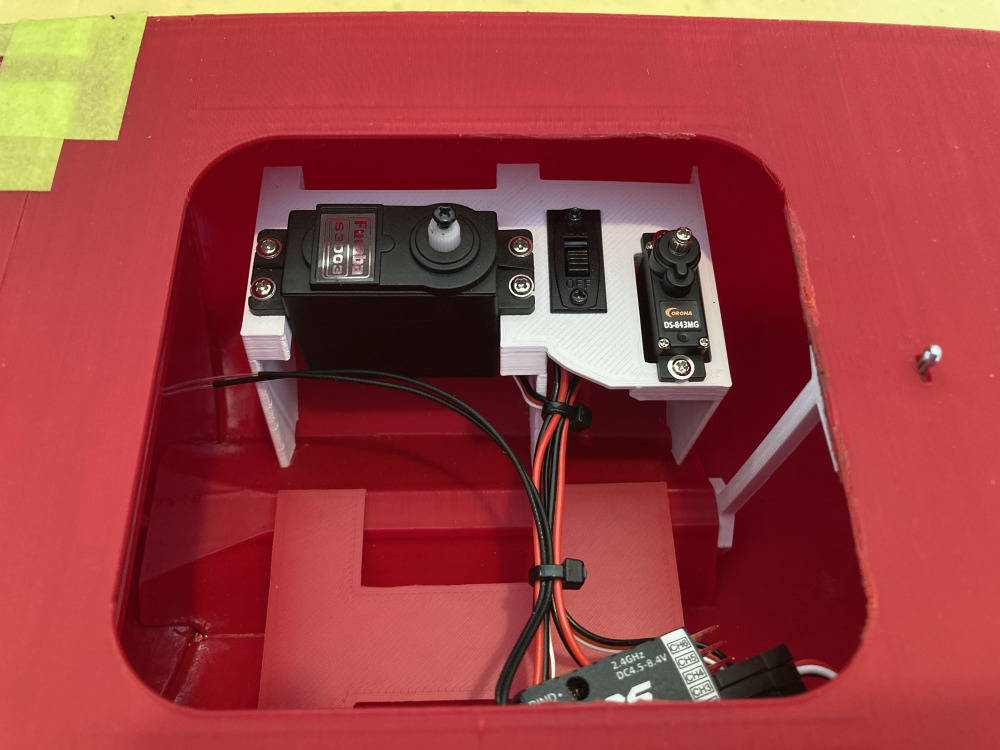
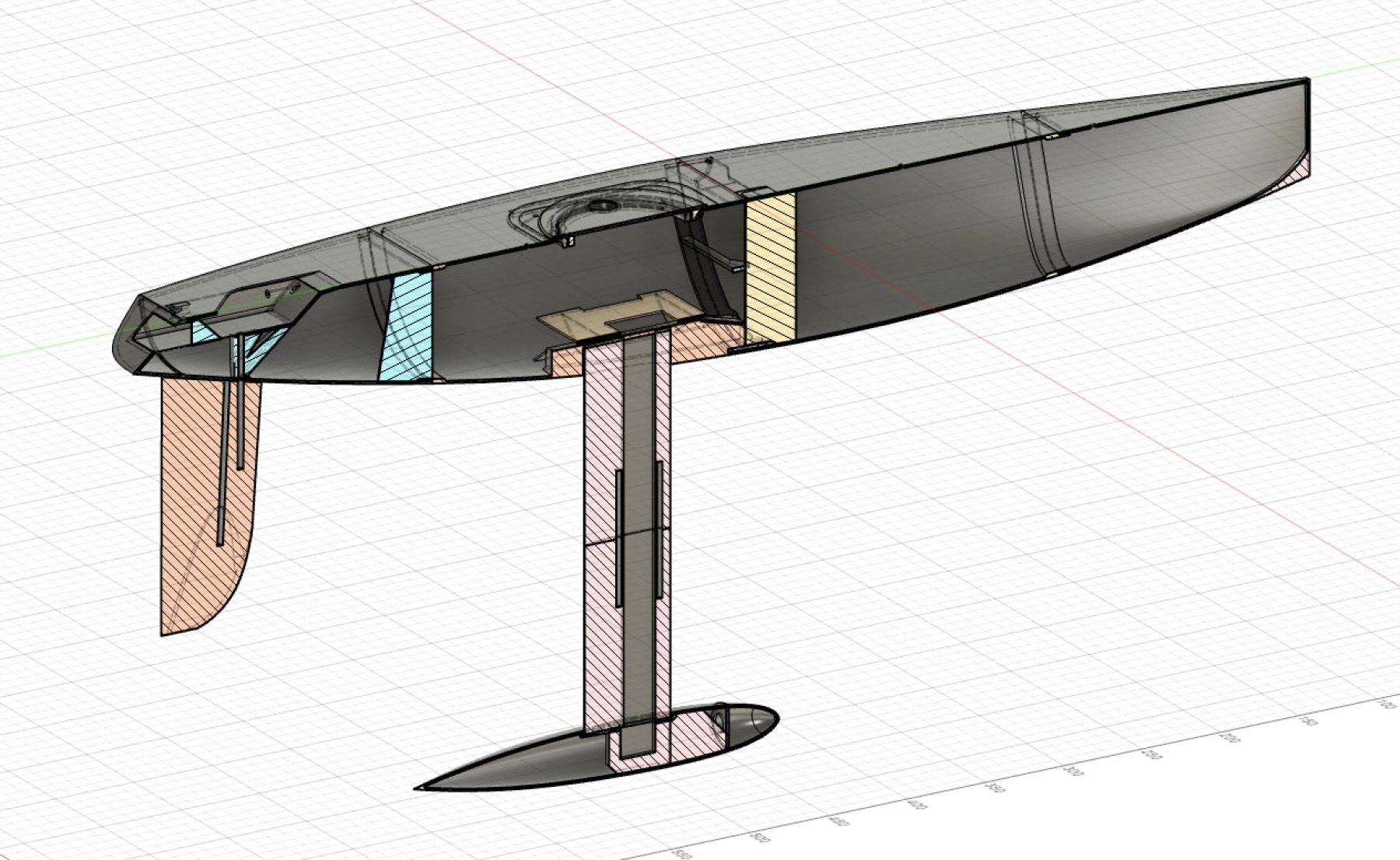
Printed Parts
The majority of the boat is printed including all rig components. This is printed from a spool of eSun PLA+ cold white. The bulb is filled with lead shot, it's a 2 piece component.
You can mix and match colours for different parts of the boat if you like. A white keel and rudder looks great imo, then maybe red hull and bulb with a white hatch cover.
You can even get PLA that is a gradient of colours or even metallics. Get creative!
You could fair the surface and then sand down and spray to get a pro finish or leave natural printed texture for a fast track build. A shiney smoother surface should in theory sail faster. But it would add weight to the hull possibly cancelling out any gains made. It would look awesome and professional.
I have not sealed the PLA+ with resin, it is straight off the printer. Hull joins with CA Superglue, keel araldyte epoxied into the slot. I sail in salt water and find brass rod or plastic is best for the rudder servo control rod. Anything else will corrode quickly. Stainless steel split pins also if sailing in the sea are a good idea.
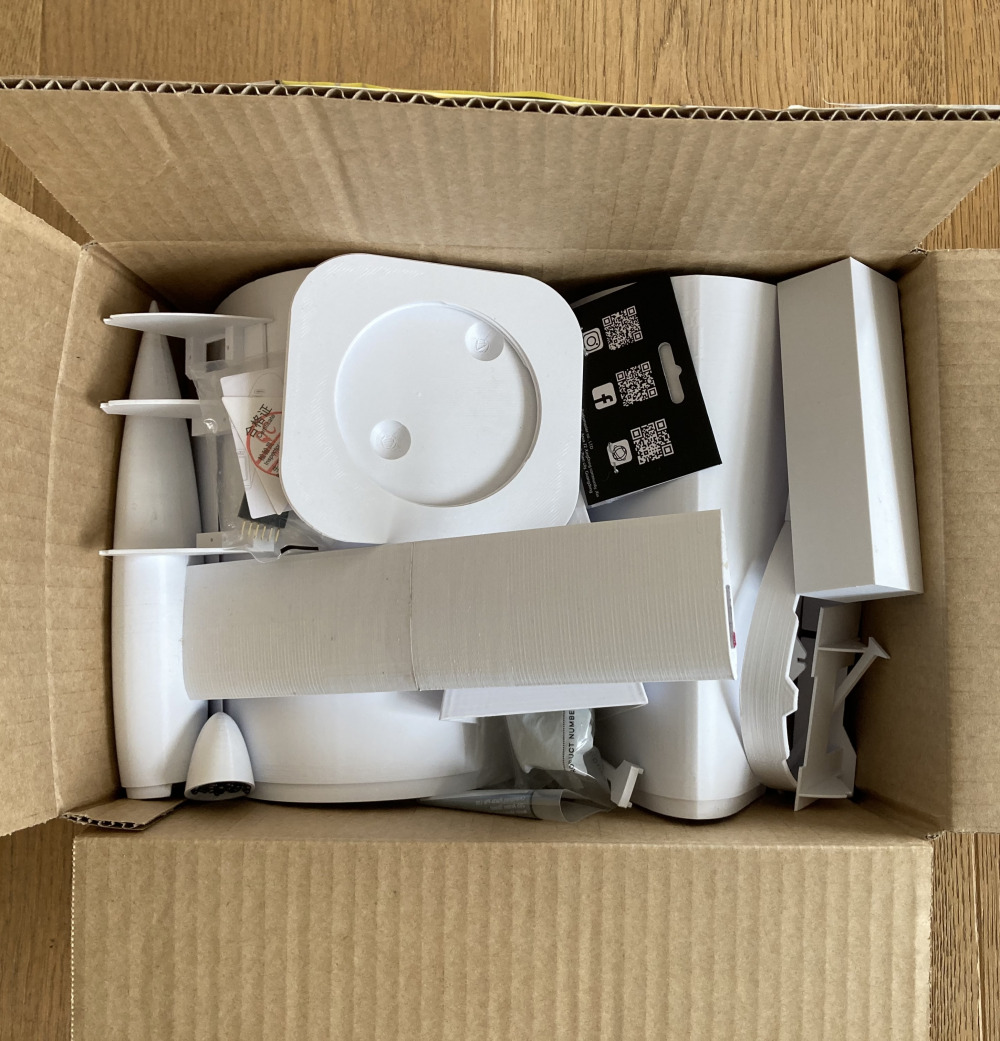
Racing Sparrow Blog
We share tips and stories from the model boat building community. Read all blog posts